Table of Contents
In the competitive world of fashion and luxury goods, efficient inventory management is crucial for maintaining smooth operations and customer satisfaction. For Cashmere Stories in Germany, optimizing sales and order processing for their premium cashmere products ranging from clothing to accessories has been a top priority.
To address these needs, Katmatic has successfully implemented an RFID-enabled inventory management system for the Stoxx Sales project. This innovative solution ensures seamless tracking of both incoming and outgoing orders, enhancing the accuracy and efficiency of inventory processes. By integrating advanced technology, Cashmere Stories can now manage their inventory with unprecedented precision, ensuring that their high-quality cashmere products are always in the right place at the right time.
Project Background
Objective: To optimize sales and order processing for Cashmere Stories, encompassing clothing, accessories, and related items. The goal is to ensure seamless and precise tracking of both incoming and outgoing orders, leveraging cross-platform development to provide a unified user experience across different devices. This application will integrate RFID technology for automated tracking and the Ninox API for database management, ensuring real-time information and improved visibility throughout the inventory management process.
Requirements: An efficient inventory management system that provides real-time tracking, integrates with sales and order processing systems, and enhances overall accuracy in monitoring stock levels.
Challenges with Traditional Inventory Management Systems
Manual Tracking: Traditional systems often rely on manual entry, which can lead to inaccuracies and delays in inventory updates.
Lack of Real-Time Information: Inability to provide instant updates on stock levels and order statuses, resulting in potential stockouts or overstocking.
Integration Difficulties: Challenges in syncing inventory data with sales and order processing systems, leading to inefficiencies and data discrepancies.
Limited Visibility: Difficulty in tracking the movement of inventory items across different stages, affecting overall operational efficiency.
Technology Stack and implementation
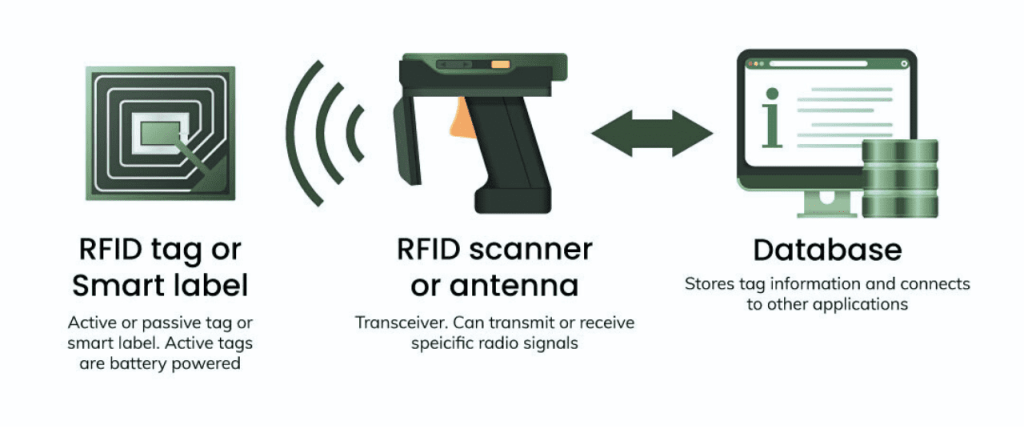
Implementation: RFID (Radio Frequency Identification) technology was utilized to automate inventory tracking by using RFID tags and readers. This technology enables real-time data capture and updates, reducing manual errors and enhancing the accuracy of inventory management. It provides seamless tracking of both incoming and outgoing orders, optimizing the sales and order processing for Cashmere Stories.
Choice: The Ninox ERP was selected for its robust database management and integration capabilities. It provides a flexible platform for handling complex data structures and ensures seamless integration with other systems, maintaining consistency and reliability in inventory data. This choice facilitates efficient data processing and enhances the application’s overall functionality.
Utilization: The .NET MAUI (Multi-platform App UI) framework was employed for the development of the cross-platform mobile application. This framework supports both backend services and front-end user interface development, allowing for the creation of scalable and responsive mobile applications. Its cross-platform capabilities ensure a unified experience across different devices, enabling seamless and precise tracking of inventory and enhancing user interaction with the application.
Key Features of the Stoxx Sales Mobile App
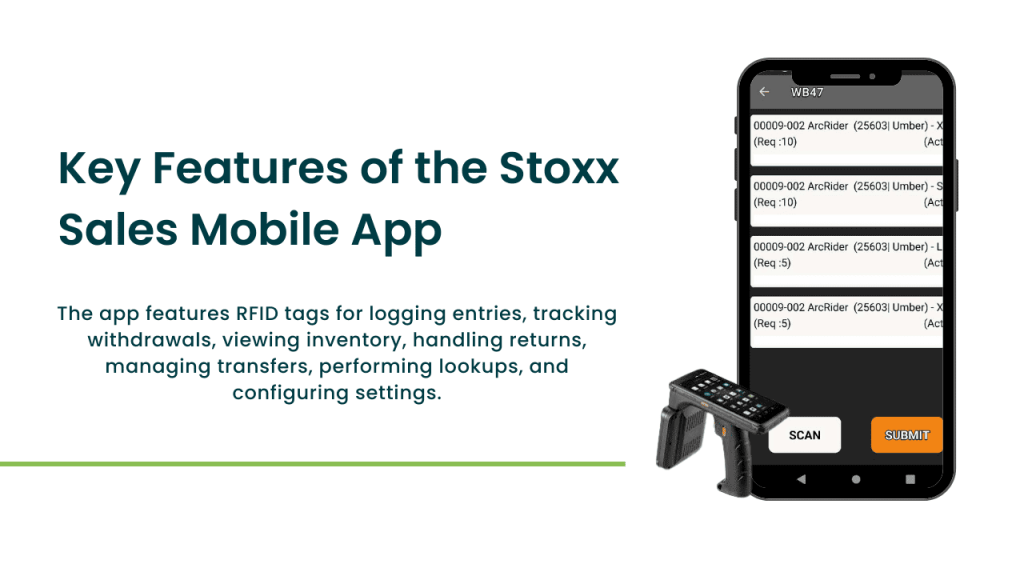
- Automatically logs new inventory items by scanning RFID tags, reducing manual input and errors.
- Updates inventory records in real-time for outgoing items using RFID scanning, ensuring accurate stock tracking.
- Provides real-time data on stock levels, item locations, and status for effective inventory management.
- Manages returned items by scanning and updating inventory records accurately.
- Tracks and records inventory movements between locations or departments using RFID technology.
- Allows searching and retrieving information about specific inventory items for quick checks and enhanced efficiency.
- Offers configuration options to customize the app, adjust RFID reader settings, and manage user permissions.
Benefits for Businesses
Real-Time Inventory Tracking
Accuracy: RFID technology ensures precise and immediate updates on inventory levels, reducing manual errors and discrepancies.
Visibility: Provides up-to-the-minute visibility into stock levels and order statuses, helping businesses make informed decisions.
Improved Efficiency
Automation: Automates inventory management tasks, minimizing the need for manual data entry and reducing labor costs.
Streamlined Processes: Integrates seamlessly with sales and order processing systems, speeding up order fulfillment and stock replenishment.
Data Management
Integration with Ninox API: Facilitates efficient handling of complex data structures and ensures consistency across different systems.
Reliable Reporting: Offers comprehensive reporting and analytics capabilities, helping businesses monitor performance and make data-driven decisions.
Cost Savings
Reduction in Errors: Minimizes costly errors associated with manual tracking and inventory discrepancies.
Operational Costs: Reduces the need for extensive manual labor and associated operational costs by automating routine tasks.
Scalability
Adaptability: The application is designed to scale with business growth, accommodating increasing inventory volumes and more complex operations.
Future-Proof: Built with flexibility in mind, allowing for easy integration of future enhancements and new technologies.
Better Inventory Control
Minimized Stockouts and Overstocking: Real-time data helps prevent stockouts by providing timely updates on low stock levels and avoiding overstocking by maintaining optimal inventory levels.
Conclusion
In conclusion, the Stoxx Sales project has transformed inventory management for Cashmere Stories with its innovative use of RFID technology, the Ninox API, and the .NET MAUI framework. This cross-platform mobile application delivers real-time tracking and seamless integration, addressing the inefficiencies of traditional systems and enhancing overall accuracy and efficiency. Katmatic’s commitment to leveraging cutting-edge technology underscores its role in advancing inventory management solutions. For those looking to revolutionize their inventory processes, Katmatic is poised to deliver exceptional results and drive future innovations.
The detailed account of how Katmatic utilized RFID technology to enhance inventory management for Stoxx Sales is both impressive and informative. Your insights into the implementation process and the benefits realized are incredibly valuable for understanding the impact of RFID in modern inventory systems. Thank you for sharing such a compelling and practical success story!